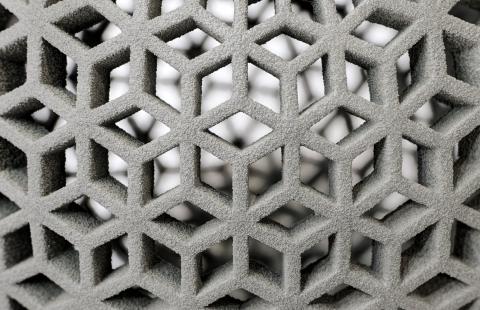
AM3L: shock-absorbing metallic structures
The start-up AM3L innovates in the field of shock absorption with its innovative metallic structures for a range of sectors, including energy and aeronautics. With production scheduled to begin in 2025, AM3L is also committed to sustainable alternatives, developing new-generation tools that allow manufacturers to create competitive biodegradable packaging, reducing plastic use.
In 2014, Hicham Maskrot, a researcher at CEA Paris-Saclay, became laboratory manager and founded the Samanta platform to focus on innovative processes for materials research. Five years later, Timothée Delacroix joined the laboratory to complete his PhD on metallic processes. "I suggested we created a start-up because we had identified a clear industry need for mechanical metamaterials, particularly for shock absorption and industrial filtration," explains Hicham Maskrot.
In 2023, Timothée won the French government's innovation contest, the i-PhD competition. In October 2023, the pair, together with the French Alternative Energies and Atomic Energy Commission (CEA), officially launched AM3L. AM3L serves as a bridge between the research conducted at CEA Paris-Saclay on additive manufacturing processes and the market. We are firmly established on the Paris-Saclay site, which is an incredibly conducive environment for our development," enthuses the co-founder. Today, the young company employs five people and is incubated at IncubAlliance Paris-Saclay. It plans to recruit five more employees by 2025, and expand the workforce to 30 by 2028.
The start-up has carved a niche in the market with materials that offer multiple advantages: lightweight, repeatable and fast. "Current solutions are limited in terms of design and often face challenges around bulk and weight. A certain repeatability of mechanical behaviour is crucial for safety, and that's what we offer. Our process is traceable layer by layer, as everything is digital, which is very important for industrial customers. Finally, whereas it takes several days to produce a mechanical metamaterial in a foundry, we can manufacture a shock absorber in 24 hours in a single step," adds the co-founder. AM3L currently holds twelve patents.
3D printer printing metal. Laser sintering machine for metal. Metal is sintered under the action of laser into shape. DMLS, SLM, SLS. Modern additive technologies 4.0 industrial revolution. Sparks
Shock absorption with metallic metamaterials
The start-up's technology is based on the Laser Powder Bed Fusion (LPBF) process. This technology spreads thin layers of metal powder one top of each other, with selective consolidation of the material by one or more lasers between each layer. The start-up is a partner of Nikon SLM Solutions, which provides open machines, that allow the teams to modify all machine parameters. This flexibility enables both research and production of 3D-architectured objects. "For this type of process, over 160 variables come into play and we can manage them all. We have total control over the raw materials and know which variables to choose. We combine the raw material, the process parameters, the design of the basic structure and its spatial distribution to achieve the performance expected by our customers," explains Hicham Maskrot.
As well as understanding and exploiting the parameters of its machines to perfection, the start-up also produces customised parts with innovative designs. "We create digital models with optimised structures and adapt the shapes to existing devices," adds the co-founder. He continues: "This combination of raw materials management, parameter control and design means that we can produce high-performance materials. Our real added value lies in our expertise across the entire process."
Products manufactured by the start-up can also be enhanced with surface treatments if requested by the customer. Thin-film deposits or coatings can be applied using gaseous or physical precursors.
A wide range of customers
The parts created by the young company are primarily designed to protect the integrity of devices in the event of impact, including containers for nuclear waste storage, stratospheric balloons in aeronautics, drones and goods transport. The company has already qualified its shock absorbers for use in the CEA's nuclear storage platform in Marcoule, in the Gard region. While used shock absorbers can technically be recycled and converted back into metal powder, in the case of nuclear waste, the structures are contaminated, requiring them to be treated as special waste.
AM3L has already generated a turnover and secured customers in the energy, transport and aeronautics sectors through this business. In the coming years, it plans to adapt its designs for the transport of dangerous or fragile goods, rail and defence. While the company's current customers are based in France, it aims to expand internationally by 2027. The start-up is in the process of setting up its first production facility at the Ferme du Moulon farm in Gif-sur-Yvette (Essonne), managed by the Paris-Saclay Public Development Institution (EPA). It is self-funding the entire project and production is due to start in February 2025 with 500 to 1,000 parts expected to be produced annually from the first year.
In addition to its shock-absorbing structures, AM3L is manufacturing custom filtration media, although this development area is less of a priority. These complex filters are designed for applications ranging from air and water purification to separation processes in industrial applications. It is also creating components for hydrogen production in fuel cells.
Expanding into new markets
At the same time, AM3L is exploring porous tooling. "Our idea is to limit plastic use by offering packaging manufacturers 2.0 moulds that enable the use of biodegradable raw materials instead of polymer resins. This approach has a positive environmental impact and reduces greenhouse gas emissions," explains Hicham Maskrot. AM3L is co-developing packaging solutions with other companies, whose names have not yet been revealed. In particular, it produces tools for pressing cellulose into packaging. The moulds optimise the release of steam and water during the pressing of biobased materials, while offering design flexibility through the 3D technology.
Although the start-up has not yet raised any funds, it plans a fundraising round in 2026 to finance a second production facility in Île-de-France. However, it has received support from Bpifrance via the French Tech Emergence grant. "We have also benefited from CEA's Magellan programme and the HEC Challenge + programme to learn how to manage the commercial and entrepreneurial aspects of the start-up. Additionally, we are supported by the public research incubator IncubAlliance and the private accelerator Wilco," concludes Hicham Maskrot.